Soldering Machines: The Essential Guide To Reliable Electrical Connections
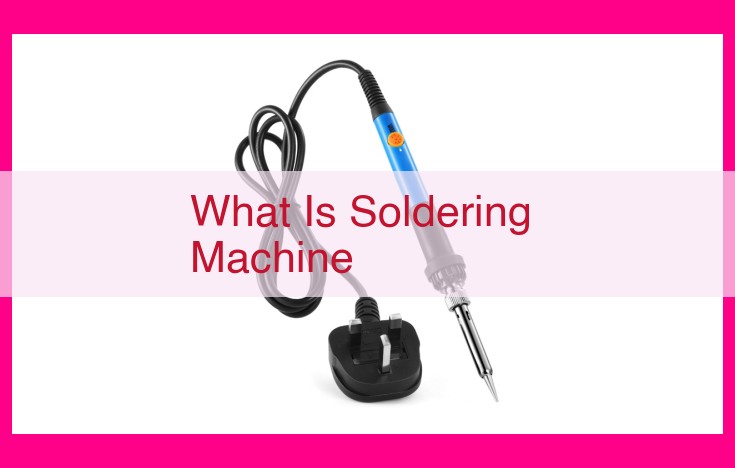
Soldering machines are specialized tools used to create strong and reliable electrical connections by joining metal surfaces with a solder alloy. These machines typically feature a controlled heat source, such as a soldering iron or hot air gun, that melts the solder and allows it to flow between the metal surfaces. Soldering is widely used in various industries, including electronics, automotive, and telecommunications, for assembling printed circuit boards, connecting wires, and repairing components.
Soldering: The Art of Connecting Electronics
In the intricate realm of electronics, soldering stands as a vital technique that has revolutionized the way electrical connections are made. It is a process that involves joining two metal surfaces using a low-melting point alloy called solder.
Soldering finds its applications in a diverse range of industries, from aerospace to automotive, and from medical device manufacturing to telecommunications. It is the key to creating reliable and durable connections in circuit boards, electronic devices, and other intricate components.
Equipment and Materials for Soldering: Mastering the Art of Joining
In the realm of electronics, soldering stands as an indispensable technique that unites components, creating a seamless flow of energy. It’s a skill that empowers engineers to breathe life into complex circuits, from the tiny microchips in our smartphones to the vast wiring systems that power our cities.
To embark on this soldering journey, you’ll need an arsenal of essential tools and materials, each playing a crucial role in ensuring precise and durable connections. Let’s delve into the secrets of these soldering essentials:
Solder: The Bonding Agent
Solder is the lifeblood of any soldering operation. This metallic alloy, typically composed of tin and lead, liquefies when heated, forming a strong bond between metal surfaces upon cooling. Different types of solder, varying in composition and melting point, are tailored for specific applications.
Flux: The Invisible Helper
Flux is the unsung hero of soldering. This chemical compound removes oxides from metal surfaces, enabling the solder to effortlessly wet and adhere. Without flux, your soldering joints would be brittle and prone to failure.
Soldering Iron: The Heat Source
The soldering iron is the workhorse of the soldering process. This heated tool melts the solder, allowing you to precisely apply it where needed. Soldering irons come in various wattages and tip shapes, optimized for different applications.
Other Essential Tools
In addition to these core materials, a few other tools can enhance your soldering experience:
- Desoldering Pump: A vacuum device that removes solder from existing joints, allowing for rework or repairs.
- Solder Wick: A braided copper wire that absorbs molten solder, providing a convenient way to clean up excess solder or bridge gaps.
- Helping Hands: A movable clamp that holds your workpiece in place, freeing up your hands for more intricate soldering tasks.
Soldering Processes: Techniques and Applications
Soldering, the art of joining metals with a lower-melting-point alloy, finds widespread application across industries, from electronics manufacturing to jewelry making. To master this technique, understanding the various soldering processes is crucial.
Hand Soldering: Precision and Control
Hand soldering, the most fundamental technique, involves manually applying solder to the joint using a soldering iron. This method offers precision and control, making it ideal for intricate assemblies and repairs. The soldering iron’s temperature and tip shape can be customized to suit specific needs.
Wave Soldering: Mass Production Efficiency
For high-volume production, wave soldering is employed. Here, a solder wave passes over a conveyor belt carrying the circuit board, creating soldered joints simultaneously. This automated process ensures high throughput and reduces human error.
Reflow Soldering: Advanced Connections
Reflow soldering involves placing solder paste on the circuit board and then exposing it to controlled heat. This process melts the solder, creating permanent connections between electronic components. Reflow soldering is widely used in the assembly of surface-mount devices.
Choosing the Right Technique
The selection of a soldering process depends on several factors, including the volume of production, the type of assembly, and the desired precision. Hand soldering is ideal for small-scale, precise applications, while wave soldering suits mass production. Reflow soldering offers advanced connectivity for surface-mount components.
Soldering processes, whether hand soldering, wave soldering, or reflow soldering, provide versatile methods for joining metals. Understanding these techniques empowers individuals to create reliable and durable connections in various industries. By selecting the appropriate process and following best practices, soldering can enhance the functionality and longevity of electronic assemblies.
Characteristics of Soldered Joints
Understanding the characteristics of soldered joints is crucial for ensuring the reliability and performance of electronic assemblies. Several factors influence the quality of these joints, including:
Solderability:
- Solderability refers to the ability of a metal surface to form a strong bond with solder.
- It is influenced by factors such as the metal’s surface condition, composition, and temperature.
- Good solderability ensures a secure and reliable connection.
Wettability:
- Wettability is the ability of solder to spread over and adhere to a metal surface.
- It is influenced by the surface tension of the solder and the presence of flux.
- Good wettability ensures a uniform and continuous solder joint.
Joint Design:
- The design of the soldered joint plays a vital role in its quality.
- Proper joint design minimizes stress and improves the strength and longevity of the connection.
- Factors such as joint geometry, solder volume, and thickness all contribute to joint design.
Other factors that affect the characteristics of soldered joints include:
- Solder Type: Different solders have varying properties that can influence joint quality.
- Flux: Flux removes contaminants and promotes wettability.
- Soldering Technique: The soldering technique used (hand soldering, wave soldering, etc.) can impact joint characteristics.
- Environmental Conditions: Temperature, humidity, and cleanliness can affect the soldering process and joint quality.
By understanding these characteristics and optimizing the soldering parameters, engineers can ensure the reliability and longevity of electronic assemblies.
Safety Considerations for Soldering: A Journey of Caution and Protection
In the captivating world of soldering, where delicate circuits take shape and electronic dreams come to life, the pursuit of precision and efficiency should never overshadow the paramount importance of safety. As you embark on your soldering adventure, embrace a mindset of vigilance, aware of the potential hazards that lurk within this captivating craft.
Navigating the Fume Labyrinth:
As your soldering iron whispers sweet melodies, be mindful of the subtle yet insidious fumes that dance in the air. Lead, the primary ingredient in traditional solder, can wreak havoc on your health if inhaled. Ensure proper ventilation by working in well-aerated areas or investing in a fume extractor. Don a respirator mask if necessary, protecting your lungs from this unseen threat.
Mastering the Heat Symphony:
The soldering iron, a conductor of heat, demands your utmost respect. Burns are an ever-present danger, lurking at the slightest touch of carelessness. Handle the iron with insulated gloves and place it securely on a designated stand when not in use. Remember, a cool soldering iron is a happy soldering iron and a safe companion on your journey.
Electricity’s Hidden Dangers:
Electricity, the lifeblood of soldering, flows through wires and circuits with an invisible force. Electrical shock can send a jolt through your body, causing discomfort, injury, or even worse. Use insulated tools and wear protective gear to minimize the risk of contact. Always disconnect power before working on electrical devices, ensuring your safety remains paramount.
Safety Precautions: A Shield Against Risk
Embrace these safety measures to create a sanctuary of protection in your soldering workspace:
- Wear safety glasses to safeguard your eyes from flying sparks and molten solder.
- Protect your skin with heat-resistant gloves and clothing, shielding it from accidental burns.
- Maintain a clean and organized work area, minimizing clutter that could trip you or cause accidents.
- Never touch the iron tip with bare hands, as it can reach scorching temperatures.
- Store soldering chemicals and materials safely, keeping them out of reach of children and pets.
Remember, safety is not a mere afterthought but the cornerstone of every successful soldering endeavor. By adhering to these safety guidelines, you transform your soldering journey into a harmonious symphony of precision, efficiency, and unwavering protection.
Applications of Soldering: A Vital Technique in Diverse Industries
Soldering, an indispensable technique in the realm of electronics assembly, finds its applications across a myriad of industries, from aerospace to telecommunications. This process involves joining metal surfaces using a low-melting-point alloy called solder, creating permanent and reliable connections.
Aerospace Industry
In the demanding world of aerospace engineering, soldering plays a critical role in fabricating and repairing intricate electronic components used in aircraft and spacecraft. The ability to create high-quality, durable joints is paramount for ensuring the safety and reliability of these systems.
Automotive Industry
The automotive industry relies heavily on soldering for assembling electronic control units (ECUs) that manage vital vehicle functions. These miniaturized components demand precise soldering techniques to achieve the desired level of performance and longevity.
Medical Device Manufacturing
Soldering is crucial in the production of sophisticated medical devices, such as pacemakers, surgical robots, and diagnostic equipment. The precision and reliability of soldered joints are essential for the accurate functioning and safety of these life-saving technologies.
Telecommunications Industry
The telecommunications sector employs soldering for interconnecting high-speed data cables and components. These resilient connections ensure the seamless flow of information and support the ever-growing demand for reliable communication networks.
Soldering remains an indispensable technique in a multitude of industries, enabling the creation of durable, high-performance electronic systems. From the aerospace sector to medical device manufacturing, the ability to solder efficiently and effectively is key to innovation and technological advancements.