Friction Burn Duration On Shafts: Factors And Mitigation Strategies
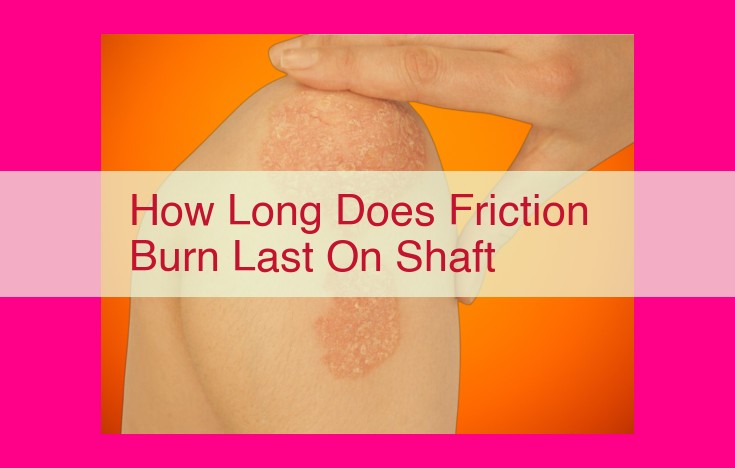
Friction burn on a shaft can last from a few seconds to several hours or even days, depending on the severity of the burn and the nature of the materials involved. The type of shaft material, friction material, lubrication, and surface roughness all influence the duration of the burn. Additionally, factors such as heat dissipation, contact pressure, and sliding velocity can further affect the longevity of the burn. Proper lubrication and maintenance practices are crucial in minimizing friction and preventing burn damage to shafts.
Friction Elements: Unveiling the Essence of Dynamic Interactions
Friction, an indispensable force that governs the interaction between surfaces, plays a pivotal role in various aspects of our lives. Understanding its underlying elements is crucial for optimizing friction performance and navigating its complexities.
Shaft Material: The Foundation of Friction
The material constituting the shaft significantly influences friction. Harder shafts generally exhibit lower friction due to their reduced surface contact area. Softer shafts, on the other hand, tend to have higher friction as they deform more easily. Selecting the appropriate shaft material for the desired friction level is essential.
Friction Material: Modulating Surface Interactions
Friction materials are meticulously designed to control friction performance. Ceramic materials offer high friction and wear resistance, making them suitable for applications requiring durability. Organic materials provide lower friction and smooth operation, ideal for applications seeking reduced friction.
Lubrication: The Friction Reducer
Lubricants, the unsung heroes of friction management, serve as an intermediary between surfaces, reducing friction and wear. Hydrodynamic lubrication creates a thin film of lubricant that separates the surfaces, while boundary lubrication provides direct contact protection. Choosing the right lubricant for the application is crucial for maximizing friction reduction.
Friction Parameters: The Invisible Forces at Play
In the world of engineering, friction is an unavoidable phenomenon that plays a significant role in the performance and longevity of mechanical systems. Understanding the various parameters that influence friction is crucial for engineers to design and optimize components to reduce friction-related problems and improve overall efficiency.
Severity of Friction
The severity of friction is a measure of the resistance encountered when two surfaces slide or roll against each other. Several factors influence friction’s severity, including load and speed. Higher loads lead to increased friction, while higher speeds can reduce friction if there is sufficient lubrication.
Surface Roughness
The roughness of the surfaces in contact directly affects the friction between them. Rougher surfaces experience more friction than smoother surfaces due to the interlocking of surface asperities. Controlling surface roughness through techniques such as polishing or honing can significantly reduce friction.
Heat Dissipation
Heat generated by friction can have detrimental effects on components. As friction increases, heat is produced, which can lead to thermal expansion, warping, and even component failure. Enhancing heat dissipation by employing cooling systems or using materials with high thermal conductivity can mitigate these effects.
Material Properties
The hardness, elasticity, and microstructure of materials significantly influence their frictional behavior. Harder materials tend to have lower friction than softer materials, while elastic materials can deform under load to reduce friction.
Surface Contact Pressure
The pressure applied to the contacting surfaces has a direct impact on friction. Higher contact pressure increases friction, as it increases the area of contact and the number of surface asperities that interlock. Optimizing contact pressure through proper component design and loading can minimize friction.
Sliding Velocity
The relative velocity of sliding surfaces affects friction. At low speeds, friction is typically higher due to adhesion between surfaces. As velocity increases, fluid mechanics come into play, and friction can decrease if there is sufficient lubrication.
Coefficient of Friction
The coefficient of friction is a numerical value that quantifies the resistance to sliding between two surfaces. It is a dimensionless quantity that provides a quick and easy way to compare the frictional properties of different material pairs. The coefficient of friction is essential for calculating friction forces and designing components where friction is a critical factor.
Friction Measurement Techniques
In the realm of friction management, accurately measuring this elusive force is paramount to preventing costly problems and optimizing system performance. Enter friction measurement techniques, a suite of tools that demystify the frictional forces at play.
Thermal Imaging: A Visual Representation of Friction
Thermal imaging harnesses the power of infrared radiation to visualize heat patterns. By converting thermal energy into color-coded images, thermal imaging provides a comprehensive map of frictional hotspots. This visual representation empowers engineers to identify areas of high friction, enabling them to pinpoint potential trouble spots before they escalate into major issues.
Infrared Sensors: Non-Contact Measurement for Real-Time Monitoring
Infrared sensors are non-contact devices that detect infrared radiation emitted by surfaces. These sensors are ideal for real-time friction measurement, as they provide continuous data without the need for physical contact. This non-invasive approach allows engineers to monitor friction levels in dynamic systems, enabling them to make adjustments on the fly.
Surface Temperature Probes: Measuring Temperature Gradients for Friction Analysis
Surface temperature probes measure temperature gradients within materials. By placing these probes on the surfaces of interest, engineers can quantify the temperature increase caused by friction. This data provides valuable insights into the frictional forces at play, allowing engineers to fine-tune their systems for optimal performance.
Related Components and Their Impact on Friction
In the realm of mechanical systems, friction plays a pivotal role, influencing component performance and longevity. To combat this inevitable force, engineers and designers rely on a trinity of components: shafts, bearings, and lubrication systems. Each element contributes uniquely to managing friction, ensuring smooth operation and extending equipment lifespan.
Shafts: The Foundation of Rotation
Shafts, the cylindrical rods that transmit power and motion, serve as the backbone of rotating machinery. Their design and material selection directly impact friction levels. Hardened steel shafts, for instance, exhibit lower coefficients of friction compared to softer materials like aluminum. Additionally, the surface finish of the shaft plays a crucial role, with smoother surfaces reducing friction and wear.
Bearings: Supporting Shafts with Reduced Friction
Bearings, the intermediaries between shafts and their supports, are designed to minimize friction while enabling smooth rotation. Rolling element bearings, like ball bearings, utilize hardened steel balls to separate the shaft from the housing, creating a low-friction interface. Conversely, fluid film bearings, such as journal bearings, rely on a thin layer of lubricant to keep the shaft suspended, significantly reducing friction and heat generation.
Lubrication Systems: The Lifeline of Friction Control
Lubrication systems play a vital role in friction management by introducing a substance (lubricant) between contacting surfaces. This oil or grease film effectively prevents direct metal-to-metal contact, reducing friction and wear. Proper lubricant selection is paramount, considering factors like viscosity, temperature range, and compatibility with the specific application.
Optimizing the Trio for Friction Control
By carefully selecting and optimizing these components, engineers can effectively mitigate friction within mechanical systems. Matching the shaft material to the application’s load and speed requirements, choosing the right bearing type for the desired friction and load capacity, and implementing a reliable lubrication system ensures a harmonious interplay of these components. This comprehensive approach not only extends equipment life but also enhances overall system efficiency and reliability.
Shafts, bearings, and lubrication systems form the cornerstone of friction management in mechanical engineering. Their design, selection, and integration determine the friction levels experienced within a system, influencing performance, longevity, and safety. By understanding the interplay of these components, engineers can effectively harness and control friction, paving the way for smoother, more efficient, and durable machinery.
Friction: A Comprehensive Guide
In the intricate world of mechanics, friction plays a pivotal role in shaping interactions between surfaces. From the whisper of a gentle breeze over the ocean to the thunderous roar of a jet engine, friction is an omnipresent force that influences the very fabric of our existence.
Understanding Friction’s Elements
To delve into the complexities of friction, we must first unravel its fundamental elements. The shaft material sets the foundation for friction’s behavior, with different materials exhibiting varying degrees of resistance. The friction material that interfaces with the shaft further modulates friction, with diverse properties affecting performance. Finally, lubricants serve as friction’s nemesis, introducing a protective layer that reduces resistance.
Quantifying Friction’s Parameters
The behavior of friction is governed by a multitude of parameters, each playing a crucial role in determining its magnitude and consequences. The severity of friction is influenced by factors like load and speed, while surface roughness directly impacts friction’s intensity. Heat dissipation is a crucial aspect, as excessive heat can lead to undesirable effects. Material properties, such as hardness and elasticity, also contribute to friction’s behavior. Contact pressure, sliding velocity, and the esteemed coefficient of friction further enrich our understanding of this multifaceted force.
Monitoring Friction: Techniques and Technologies
A plethora of techniques stand ready to unveil the secrets of friction. Thermal imaging paints a vivid picture of temperature variations, revealing friction’s hotspots. Infrared sensors provide precise measurements, while surface temperature probes offer a direct approach to discerning friction’s intensity. By harnessing these tools, we gain valuable insights into the dynamics of friction.
Related Components: A Supporting Cast
Friction’s dance is not limited to isolated surfaces; it involves a supporting cast of components. Shafts, the workhorses of mechanical systems, demand careful consideration for friction management. Bearings, the guardians of rotating shafts, play a pivotal role in reducing friction and ensuring smooth operation. Lubrication systems, the maestros of friction control, orchestrate the delivery of lubricants to critical areas, minimizing resistance.
Applications: Where Friction Meets the Real World
Friction’s influence extends far beyond the confines of theory, finding applications in a myriad of fields. Manufacturing processes, from delicate cutting to high-volume molding, rely heavily on friction management to ensure efficiency and precision. In the realm of automotive engineering, friction plays a pivotal role in the performance of engines, brakes, and transmissions. Aerospace technology demands meticulous friction control, especially in high-speed, high-temperature environments. Energy production systems, such as turbines and generators, harness friction’s power while simultaneously managing its effects.
Consequences: The Dark Side of Friction
While friction serves a vital purpose, its uncontrolled manifestations can lead to undesirable consequences. Fire hazards loom over scenarios where excessive friction generates excessive heat. Surface damage, such as wear and fatigue, can compromise the integrity of components. Component failure becomes a real possibility when friction’s destructive forces overwhelm the system’s defenses.
Allied Disciplines: A Symphony of Knowledge
Friction’s profound impact has fostered the emergence of allied disciplines that delve into its intricacies. Tribology, the science of friction, wear, and lubrication, provides a comprehensive understanding of these intertwined phenomena. Material science contributes to the development of friction-resistant materials, while lubrication technology explores innovative methods for reducing friction’s adverse effects. Together, these disciplines orchestrate a harmonious approach to friction management, unlocking new possibilities and mitigating its potential hazards.
Unveiling the Damaging Consequences of Friction
In the realm of engineering, friction plays an integral role in shaping the performance and longevity of mechanical systems. However, when friction becomes excessive, it can unleash a cascade of detrimental consequences that can endanger lives, damage equipment, and disrupt operations.
Fire Hazard: A Blazing Threat
Unchecked friction can be a spark that ignites a raging inferno. Excessive friction generates intense heat, and when the temperature rises beyond a critical point, it can trigger a fire. One classic example is the infamous “hot box” in railroad operations. When friction between the axle and the bearing becomes excessive, it can cause the axle to overheat, ignite the surrounding grease, and set the train ablaze.
Surface Damage: A Silent Erosion
Friction’s relentless assault can also inflict surface damage, gradually eroding the integrity of materials. Wear refers to the gradual loss of material due to repeated rubbing against opposing surfaces. Abrasion occurs when hard, abrasive particles scrape against a surface, creating scratches and gouges. Fatigue, on the other hand, is a form of damage that results from repeated loading and unloading, causing microscopic cracks to form and propagate, eventually leading to failure.
Component Failure: A Costly Downfall
High friction can push components to their breaking point, leading to catastrophic component failure. Extreme heat can cause materials to soften, warp, or even melt, compromising their structural integrity. Additionally, friction-induced vibration can accelerate fatigue damage, increasing the risk of sudden and potentially dangerous breakdowns.
Preventing these dire consequences requires adopting proactive measures to control friction. Engineers rely on a combination of friction management techniques, such as selecting appropriate materials, incorporating lubricants, and optimizing surface finishes. By understanding the destructive power of friction, we can harness its benefits while mitigating its risks, safeguarding the safety and efficiency of our mechanical systems.
Delving into the Friction Landscape: A Comprehensive Exploration
Friction, an ever-present force in our world, plays a pivotal role in countless aspects of science, engineering, and everyday life. Understanding its multifaceted nature is paramount to harnessing its power and mitigating its adverse effects. This comprehensive guide embarks on a journey to unravel the intricate world of friction, from its fundamental elements to its far-reaching applications.
Deciphering the Anatomy of Friction
Friction stems from the interaction between two surfaces in contact, characterized by:
- Shaft Material: The material of the rotating or sliding shaft influences friction, with harder materials exhibiting lower friction.
- Friction Material: The material on the opposing surface determines friction properties, such as grip and resistance to wear.
- Lubrication: Lubricants reduce friction by creating a protective layer between surfaces, minimizing direct contact.
Quantifying Friction’s Influence
Friction’s impact is measured through various parameters:
- Severity: High loads and speeds exacerbate friction, increasing wear and heat generation.
- Surface Roughness: Smoother surfaces reduce friction, while rougher surfaces increase it due to increased surface area contact.
- Heat Dissipation: Efficient heat dissipation reduces friction by preventing excessive temperature buildup.
- Material Properties: Properties like hardness and elasticity affect friction, with harder and more elastic materials generally exhibiting lower friction.
- Contact Pressure: Optimizing contact pressure can minimize friction while ensuring proper surface engagement.
- Sliding Velocity: Higher velocities tend to reduce friction due to reduced contact time and increased hydrodynamic lift.
- Coefficient of Friction: A dimensionless parameter quantifying friction’s magnitude, essential for design and analysis.
Measuring Friction’s Subtleties
Accurately measuring friction is crucial for quantifying and optimizing it. Techniques include:
- Thermal Imaging: Infrared cameras detect heat generated by friction, providing visual representations of friction hotspots.
- Infrared Sensors: Non-contact sensors measure surface temperature, giving real-time data on friction-induced heat.
- Surface Temperature Probes: Direct contact probes provide precise temperature measurements, allowing for detailed friction analysis.
Complementing Components
Friction is influenced by a range of components, including:
- Shafts: Design considerations like material selection, tolerances, and surface finish impact friction.
- Bearings: These support shafts, reducing friction and preventing wear, with different types suited for various applications.
- Lubrication Systems: Efficient lubrication systems control friction through proper delivery and maintenance of lubricants.
Friction in Action
Friction plays a vital role in numerous industries:
- Manufacturing: Friction is a key factor in processes like cutting, molding, and assembly, affecting efficiency and product quality.
- Automotive: Controlling friction is crucial for components like engines, brakes, and transmissions, ensuring performance, safety, and fuel economy.
- Aerospace: Friction management is critical in aircraft design, particularly in high-speed and high-temperature environments.
- Energy Production: Friction affects the efficiency of turbines, generators, and drilling equipment, impacting energy output and costs.
Consequences of Unchecked Friction
Excessive friction can have detrimental consequences:
- Fire Hazard: High friction can generate excessive heat, posing fire risks.
- Surface Damage: Friction can lead to surface wear, abrasion, and fatigue, reducing component lifespan.
- Component Failure: Uncontrolled friction can cause component failure due to excessive heat, vibration, and premature wear.
Allied Disciplines: A Collaborative Approach
Friction management draws upon multiple disciplines:
- Tribology: The specialized field focusing on friction, wear, and lubrication, providing fundamental insights and practical solutions.
- Material Science: Developing friction-resistant materials and understanding material properties that influence friction.
- Lubrication Technology: Creating advanced lubricants and lubrication methods to minimize friction and optimize performance.